KD600 series inverter in CNC lathe application scheme
Overview
CNC machine tool is the integrated application of mechanical, electrical, hydraulic, pne- umatic, microelectronics and information and other technologies as one of the electrom- echanical integration products, in the mechanical manufacturing equipment with flexible, universal, high-precision, high-efficiency "flexible" automatic production equipment, it will process the various operations and steps required and the shape and size of the workpi-ece, with digital code, Through the control medium into the numerical control device, the numerical control device to the input information processing and calculation, command control machine tool system and drive components, automatic processing of the required workpiece. The technical level of CNC machine tools and its percentage in the output and total ownership of metal cutting machine tools is one of the important indicators to mea-sure the overall level of national economic development and industrial manufacturing of a country. In recent years, the share of CNC machine tools in Chinese enterprises has incre-ased year by year, and it has been more used in large and medium-sized enterprises, and it is also generally used in small and medium-sized enterprises and even individual enterprises.
CNClathe process requirements
When the workpiece is processed by CNC lathe, the feed amount is large, the proce-ssing speed is low, and the machining process has impact load due to the uneven surface of the workpiece.
Lathefinishing, the feed amount is small, in order to ensure processing efficiency, pro- cessing speed is high.
The spindle motor is required to have low speed and high torque output, and is stab-le, and can run at high speed.
Receiving analog signals requires high linearity and low load interference.
Themotor noise is small, and the interference to the system automation equipment is small.Speed up and speed down as little as possible.
Advantages of CNClathe KD600 series products
Kd600 series high-performance vector inverter adopts advanced flux control technology, the motor torque at low speed is large, the speed accuracy is high, the price is reasonable, the function is complete, with instantaneous power failure processing and speed tracking and start again function, to ensure that the system to achieve continuous operation mechanism, to ensure that the motor is running at the highest efficiency state, therefore, Using KD600 series high-performance vector inverter instead of spindle AC servo system is the best choice for machine tool industry. KD600 series inverter has the following features:
Unique weak magnetic control technology: can be a good control of low frequency large torque motor, can run in 0 ~ 600Hz.
Fastandstable stop speed: magnetic flux deceleration stop technology can make the motor slowdown and stop in a shorter time.
Speed accuracy and stability: the linearity of speed setting is good, the accuracy of speed stability is high, and the fluctuation of speed is within 5/1000 when the load changes.
Excellent low frequency performance: Optimized PG-free vector control algorithm, low frequency 1Hz up to 150% rated torque output, to ensure strong cutting force during blank processing.
Providemultiple frequency input modes: 2 voltage sources 0 ~ 10V or -10V to +10V input, 1 current source 4~20mA or 0~20mA input.
Wide range of grid voltage application: Advanced switching power supply design can be applied to a variety of grid environments.
Exquisite production process: adopt a unique coating thickening process, the air duct is completely isolated from the internal PCB, and has strong adaptability to the harsh physical environment such as metal dust, corrosive gas, and humidity.
Built-in leakage absorption circuit greatly reduces the electric shock to the human body when the equipment housing is charged.
Basic wiring diagram
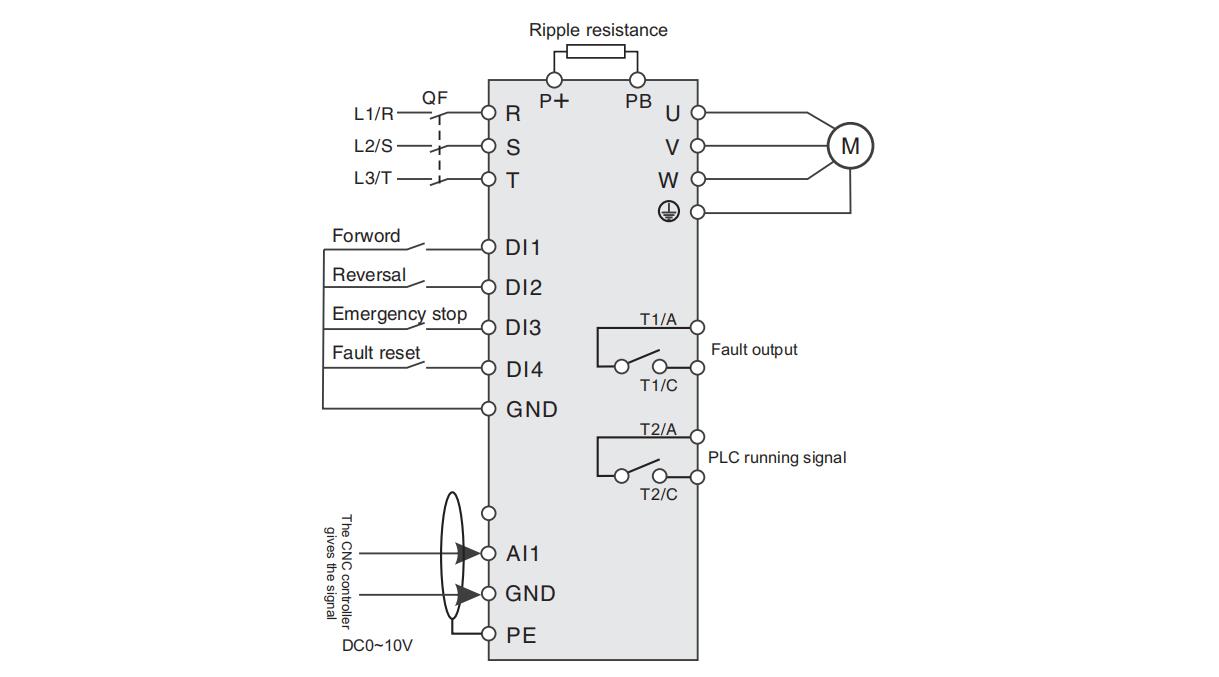
Parameter Settings and description
Debugging result
It has been proved that KD600 series high-performance vector frequency converter can fully meet the requirements of machine tool spindle control. KD600 adopts the leading PG-free vector control mode, which can smoothly output 150% torque even under low speed (low frequency) operation to meet the processing needs of different parts, and can completely replace the traditional rolling bearing spindle structure, and this spindle structure is simple, compact, and can achieve true stepless speed regulation. The speed of this spindle is controlled by an external analog signal to control the output frequency in different processing processes (e.g. Roughing, finishing, etc.) need different speed, at this time, the numerical control system can output different analog voltage signals to the inverter to achieve different speed, and the start and stop signal is also controlled by the numerical control system, which improves the degree of automation and extends the service life of the tool.
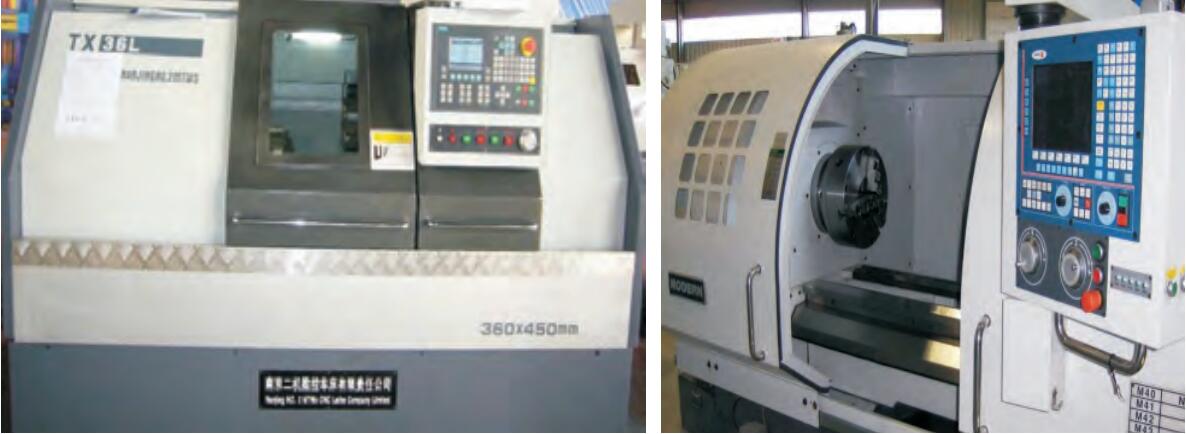