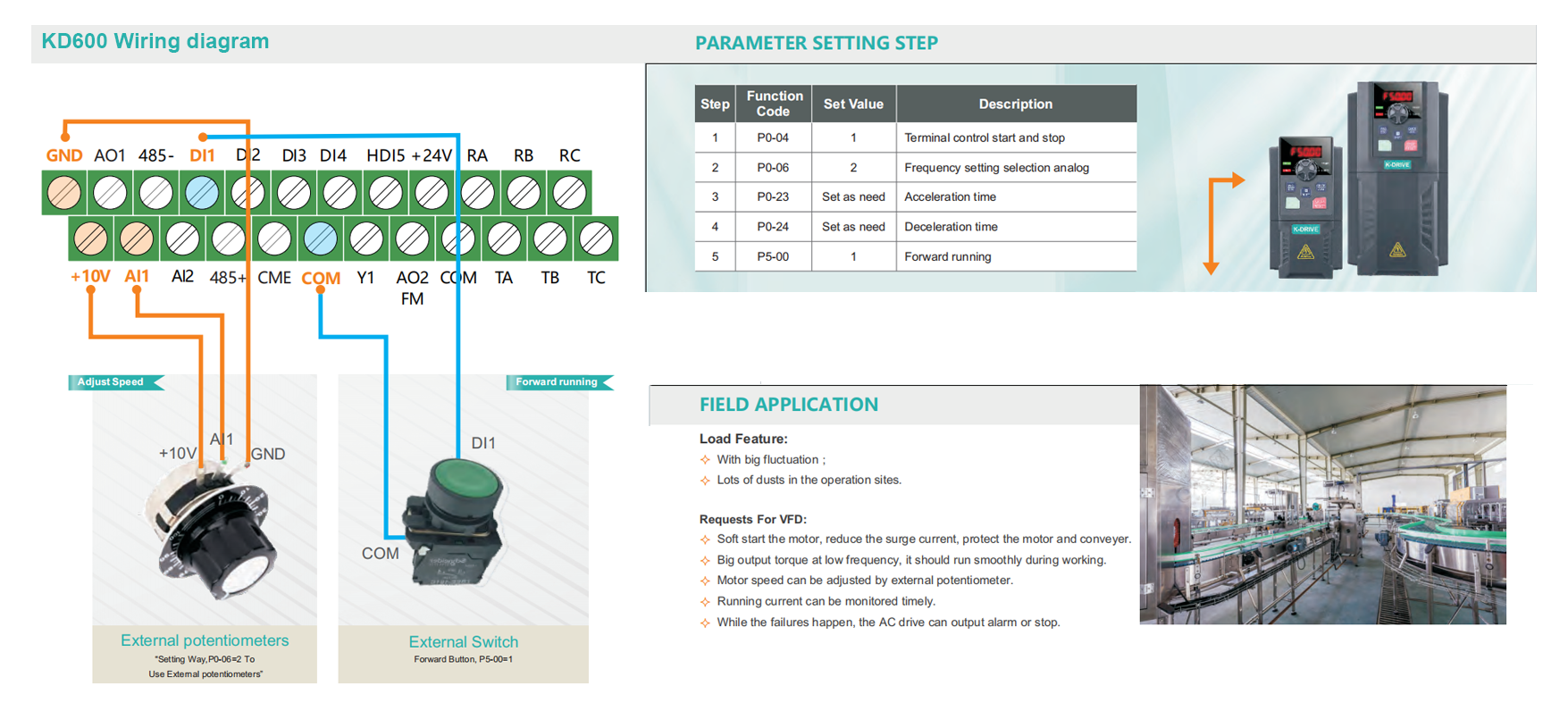
Application Background
A manufacturing plant has a conveyor belt system used for transporting finished products. Due to the different processing speeds required in various production processes, the conveyor belt needs to be able to adjust its speed flexibly to meet production demands, thereby improving overall production efficiency and product quality.
Application Case
The plant decided to use the KD600 series inverter to control the conveyor belt motor to achieve precise speed control, energy-saving effects, and ensure the reliability and safety of the system operation.
Parameter Configuration
Motor Parameters
Type: Three-phase asynchronous motor
Rated Power: 5.5 kW
Rated Voltage: 380V
Rated Frequency: 50Hz
Rated Current: 11A
Inverter Parameters
Model: KD600-4T-5.5GB
Input Voltage: Three-phase 380V
Output Voltage: Three-phase 0~380V
Output Power: 5.5 kW
Output Frequency: 0~400 Hz
Control Method: Vector control/V/F control
Overload Capacity: 150% for 60 seconds
Application Settings
Acceleration Time: 10 seconds (soft start)
Deceleration Time: 10 seconds
Maximum Frequency: 60 Hz
Minimum Frequency: 10 Hz
Speed Setting: Controlled by an external potentiometer (e.g., 0-10V)
Start/Stop Control: Controlled by an external switch
Operation Monitoring: Real-time monitoring of running current
Protection Functions: Overcurrent protection, overvoltage protection, overheat protection, undervoltage protection, fault alarm or stop
Function Parameter Settings
Step | Funtion Code | Set Value | Description |
1 | P0-04 | 1 | Terminal control start and stop |
2 | P0-06 | 2 | Frequency setting selection analog |
3 | P0-23 | Set as needed | Acceleration time |
4 | P0-24 | Set as needed | Deceleration time |
5 | P5-00 | 1 | Forward running |
System Integration
Installation and Wiring
The KD600 inverter is installed in a control cabinet. The three-phase power supply is connected to the inverter input, and the motor is connected to the inverter output. At the same time, an external potentiometer is connected to the analog input of the inverter for speed control, and an external switch is used for start/stop control of the inverter.
Commissioning and Operation
During initial commissioning, basic parameters are set, and no-load tests are conducted. After confirming there are no issues, load operation is conducted to observe whether the conveyor belt speed changes meet the set requirements and to check the operating status and protection functions of the inverter.
Control Scheme
Speed Control: The conveyor belt speed is adjusted in real-time according to different process requirements by sending analog signals (e.g., 0-10V) through the external potentiometer, ensuring continuous and efficient production.
Start/Stop Control: The conveyor belt is started and stopped via an external switch, which is simple to operate and suitable for on-site operation needs.
Soft Start: The inverter provides a soft start function, reducing surge current during motor startup, thus protecting the motor and conveyor belt.
High Output Torque: The inverter delivers high output torque at low frequencies, ensuring smooth operation of the conveyor belt during work.
Operation Monitoring: Real-time monitoring of running current ensures the motor operates within the normal current range.
Fault Protection: The inverter's built-in protection functions ensure the system automatically stops or alarms in case of abnormalities, preventing equipment damage.
Application Effect
After using the KD600 inverter, the conveyor belt system achieved flexible speed adjustment and reliable start/stop control, significantly improving production efficiency. The soft start function effectively reduced surge current during motor startup, protecting the motor and conveyor belt. Real-time monitoring of running current ensured the system operated within safe limits. The high output torque function ensured smooth operation of the conveyor belt at low speeds. The inverter's fault protection functions improved the reliability and safety of the system, safeguarding the production process.